Plastic Injection Molding Machines: A Comprehensive Guide to Technology, Applications, and Best Practices
Plastic Injection Molding Machines: A Comprehensive Guide to Technology, Applications, and Best Practices
Blog Article
Plastic injection molding machines are the backbone of modern manufacturing, enabling the mass production of intricate plastic parts with precision and efficiency. From the automotive industry to medical devices, these machines have revolutionized how we create everyday products. In this article, we’ll explore the technology behind plastic injection molding, its applications, challenges, and future trends, while also providing actionable insights for businesses and operators.
What Are Plastic Injection Molding Machines?
Plastic injection molding machines are industrial devices that transform raw plastic materials into finished products. The process involves melting plastic pellets, injecting the molten material into a mold, cooling it, and ejecting the final product. The machine consists of several key components:
- Hopper: Feeds raw plastic pellets into the machine.
- Barrel and Screw: Heats and melts the plastic.
- Mold: Shapes the molten plastic into the desired form.
- Clamping Unit: Holds the mold in place during injection.
- Ejector: Removes the cooled product from the mold.
This process is highly efficient, capable of producing thousands of identical parts in a short time. According to a report by Grand View Research, the global plastic injection molding market was valued at $12.8 billion in 2022 and is expected to grow at a compound annual growth rate (CAGR) of 4.8% from 2023 to 2030.
Types of Plastic Injection Molding Machines
There are several types of plastic injection molding machines, each suited for specific applications:
- Hydraulic Injection Molding Machines
- These machines use hydraulic systems to generate the pressure needed for injection.
- Pros: Cost-effective and capable of handling high-pressure applications.
- Cons: Less energy-efficient and bulkier compared to electric models.
- Electric Injection Molding Machines
- Electric motors drive the injection process, offering greater precision.
- Pros: Energy-efficient, quieter, and ideal for high-precision parts.
- Cons: Higher upfront costs.
- Hybrid Injection Molding Machines
- Combining hydraulic and electric systems, hybrids offer a balance of power and efficiency.
- Pros: Reduced energy consumption and improved performance.
- Vertical vs. Horizontal Machines
- Vertical Machines: Ideal for insert molding and smaller parts.
- Horizontal Machines: Better suited for high-volume production.
Applications of Plastic Injection Molding Machines
Plastic injection molding is ubiquitous across industries:
- Automotive: Dashboards, bumpers, and interior components are commonly produced using this method.
- Medical: Syringes, IV components, and surgical tools require the precision and sterility that injection molding provides.
- Consumer Goods: From toys to kitchenware, injection molding delivers durable and cost-effective products.
- Electronics: Casings, connectors, and other components rely on the precision of injection molding.
- Packaging: Bottles, caps, and lids are mass-produced using this technology.
A study by Market sand Markets highlights that the automotive sector accounts for the largest share of the injection molding market, driven by the demand for lightweight and durable components.
Advantages of Plastic Injection Molding
The popularity of plastic injection molding stems from its numerous benefits:
- High Efficiency: Capable of producing thousands of parts per hour.
- Precision: Complex geometries and intricate designs can be achieved with high accuracy.
- Material Versatility: Works with thermoplastics, thermosets, and elastomers.
- Cost-Effectiveness: Low per-unit cost for large-scale production.
Challenges and Considerations
Despite its advantages, plastic injection molding comes with challenges:
- High Initial Investment: Machinery and mold design can be expensive.
- Environmental Concerns: Plastic waste and recycling remain significant issues.
- Maintenance Costs: Regular upkeep is essential to ensure optimal performance.
To address environmental concerns, many companies are adopting sustainable practices, such as using biodegradable plastics and recycling post-consumer waste. For example, Coca-Cola has committed to using 50% recycled materials in its packaging by 2030.
Innovations in Plastic Injection Molding
The industry is evolving rapidly, driven by technological advancements:
- AI and IoT: Predictive maintenance and real-time monitoring are improving efficiency and reducing downtime.
- Sustainable Practices: Biodegradable plastics and closed-loop recycling systems are gaining traction.
- 3D Printing Integration: Rapid prototyping using 3D printing is reducing development time.
- Energy-Efficient Machines: Newer models consume less energy, reducing operational costs.
According to a report by McKinsey & Company, the adoption of smart manufacturing technologies could reduce production costs by up to 20% by 2025.
Best Practices for Operating Plastic Injection Molding Machines
To maximize efficiency and product quality, follow these best practices:
- Regular Maintenance: Clean and calibrate machines to prevent breakdowns.
- Operator Training: Ensure staff are well-trained in machine operation and safety protocols.
- Process Monitoring: Control parameters like temperature, pressure, and cycle time.
- Quality Control: Implement rigorous testing to maintain consistency.
Future Trends in Plastic Injection Molding
The future of plastic injection molding is bright, with several trends shaping the industry:
- Automation: Increased use of robotics for loading, unloading, and assembly.
- Sustainability: Development of eco-friendly materials and processes.
- Smart Manufacturing: Integration of AI, IoT, and data analytics for real-time optimization.
- Emerging Markets: Expansion into regions like Asia-Pacific, where manufacturing is booming.
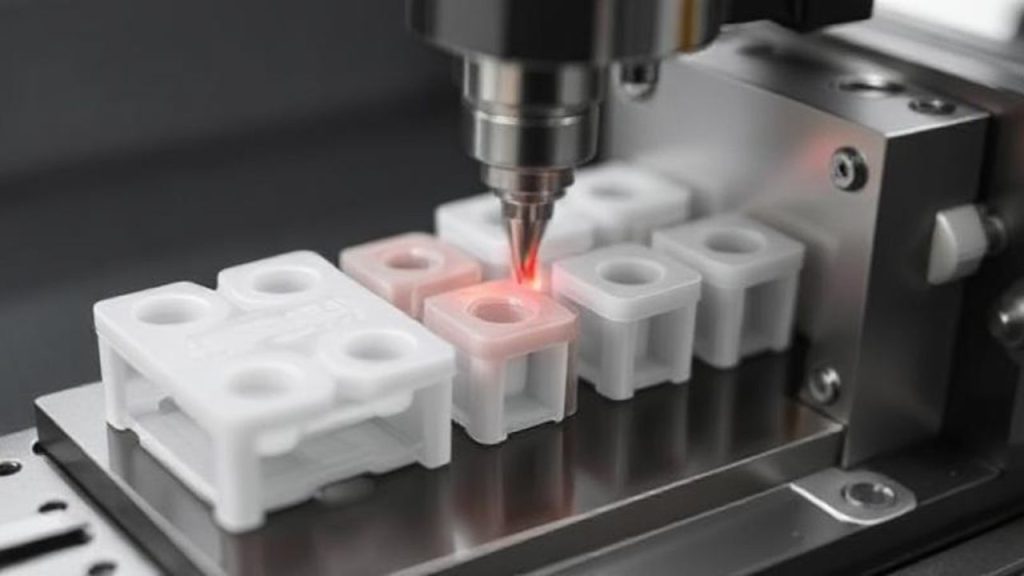
Conclusion
Plastic injection molding machines have transformed manufacturing, enabling the production of high-quality, cost-effective products across industries. As technology advances, the industry is becoming more sustainable and efficient, paving the way for a greener future. By adopting best practices and staying informed about trends, businesses can harness the full potential of this remarkable technology.
Report this page